Is our healthcare system broken?
If you were to describe the healthcare industry in the United States to an extraterrestrial, you might start by explaining it is a complex, heavily managed system with a significant private insurance component alongside public programs like Medicare and Medicaid. The result is a mixed bag, encompassing hospitals, pharmaceuticals, clinics, and other healthcare providers, all operating under a fragmented system with varying levels of regulation across the 50 states. Despite all of this, patients from around the world seek treatment here because of its cutting-edge technology, quality of care and prospect of recovery.
But there is always room for improvement. Getting back to our initial question, it can be said there is a fair amount of “waste” being generated throughout the healthcare industry, which leads to both patient dissatisfaction and healthcare worker frustration. Some examples of waste, which you can think of as defects or errors, are:
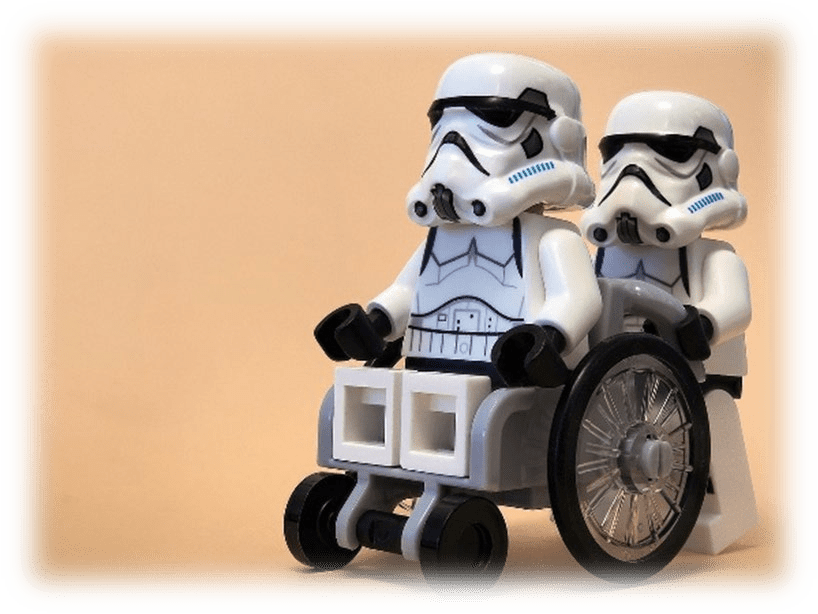
- Patients waiting in reception during follow-up visits
- Moving patients between check-in, reception, screening, labs, X-rays, and private rooms
- Administering unnecessary tests that prolong hospital stays
- Maintaining excessive inventory, risking excess cost and expiration
- Healthcare staff updating medical records off-duty
- Lack of available expertise and care due to suboptimal resource utilization
One method to eliminate the defects is to implement a Lean program. That is, actively seek out waste and drive it OUT.
Lean encourages a culture where all staff members, from frontline nurses to top management, are involved in identifying areas for improvement and implementing changes. This collaborative approach ensures that improvements are sustainable, and that the hospital can adapt to changing industry demands.
Lean also focuses on enhancing the patient’s experience. By improving processes and reducing waste, hospitals can provide a smoother and more pleasant experience. This can lead to higher patient satisfaction and better health outcomes.
Moreover, Lean practices can lead to significant cost savings. While the primary goal of Lean is not cost-cutting, the elimination of waste and improved efficiency often results in reduced operational cost. This can free up resources to reinvest in patient care and other critical areas.
It must be noted that in healthcare, unlike some other industries, the consequence of applying an improper process is critical because it involves an actual person’s well-being, and potentially loss of life. For this reason, adopting Lean (or Six Sigma or another Operational Excellence methodology) is often not prioritized. This is why unless the entire hospital embraces Lean thinking, from the CEO down to the frontline nurses, it is highly unlikely that consistent gains will be sustained.
The lean approach is often described as a “Bottoms-Up” approach, meaning the head of the company serves the frontline personnel, who in turn serve the patient. Commitment starts at the very top of the organization through the championing of management objectives. Following this, all staff become involved in helping to redesign processes that reduce waste and ultimately improve the quality of care.
Because running a hospital is complicated work, there are many areas of opportunity, which begs the question, “Where do we start?” In order to select an area of opportunity, you will look for areas with the biggest pain – no pun intended. We start here!
attended to with diligence.” – Abigail Adams
When implementing Lean concepts in a hospital setting, there are some key considerations. First and foremost, patient experience is always the priority when selecting projects. Any improvement must be focused on ensuring improvements directly benefit the patient’s journey.
This type of learning takes work and dedication. The general improvement methodology follows a 5-step problem solving approach:
Step | Description |
---|---|
Define | Describe what is happening and the pain-points |
Measure | Identify the biggest opportunities for improvement |
Analyze | Study the data for root causes and prioritize them |
Improve | Brainstorm ideas and implement pilot studies; learn, revise |
Control | Document the solutions and establish control plans |
Because of the complex nature surrounding healthcare data, of importance is the use of proper data collection efforts. These must ensure baseline performance is accurately captured and enable the team to identify the root causes of the pain points. Finally, cross-functional participation and collaboration is vital. This includes clinicians, nurses, doctors, administrators, support staff, and service providers. The engagement of Subject Matter Experts (SMEs) is essential to identifying optimal solutions efficiently.
Champion and Sponsor Training is designed to guide individuals in supporting Lean transformations within their organizations. It covers various aspects, including the roles of Champions and Sponsors, the history and application of Lean principles, practical examples and hands-on exercises. It is also important for leaders to understand the role of leadership in continuous improvement efforts and the need for perseverance and a long-term perspective.
The lean approach requires a set of principles designed to move from the AS IS state to an evolving, improved state through a series of continuous improvement steps.
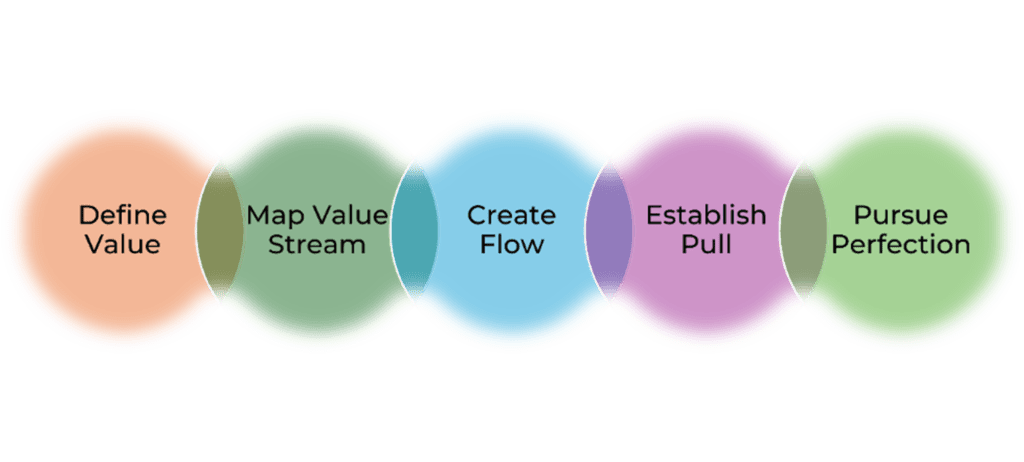
These concepts are often misunderstood, especially when they are applied to healthcare. “Lean Thinking” is often mixed up as a way of cost cutting. But this is far from the truth because lean is more about creating value by eliminating the underlying burdens that patients and staff experience every day.
Training participants are introduced to various Lean tools and techniques:
Defining Value
Value stream mapping
Identifying Waste
Leveraging the knowledge of front-line employees
Understanding and addressing root causes
Implementing pull systems
The term “Lean” is a label which is less important than its concept and the overall strategy it represents. This methodology has been tested and proven in countless other industries. Successful Lean organizations focus on sustaining higher levels of safety, efficiency, and quality. These in turn lead to higher patient satisfaction and employee morale, which leads to better financial performance because redesigning unnecessary tasks and workflows to improve care usually minimizes wasted time and other resources. This in turn frees up everyone to focus on the highest value generating activities for patients.